An HDPE liner welding machine is a specialized tool designed to join HDPE liner sheets together. These machines use heat or chemical bonding techniques to create strong, leak-proof seams. They are essential for applications where containment and waterproofing are crucial, such as pond liners, landfill caps, and industrial containment systems.
1. What Is HDPE Liner Welding Machine?
An HDPE liner welding machine joins HDPE liner sheets. It uses heat or chemical bonding to create strong, leak-proof seams. These machines are crucial for containment and
They ensure high-quality, durable welds in applications like pond liners and landfill caps.
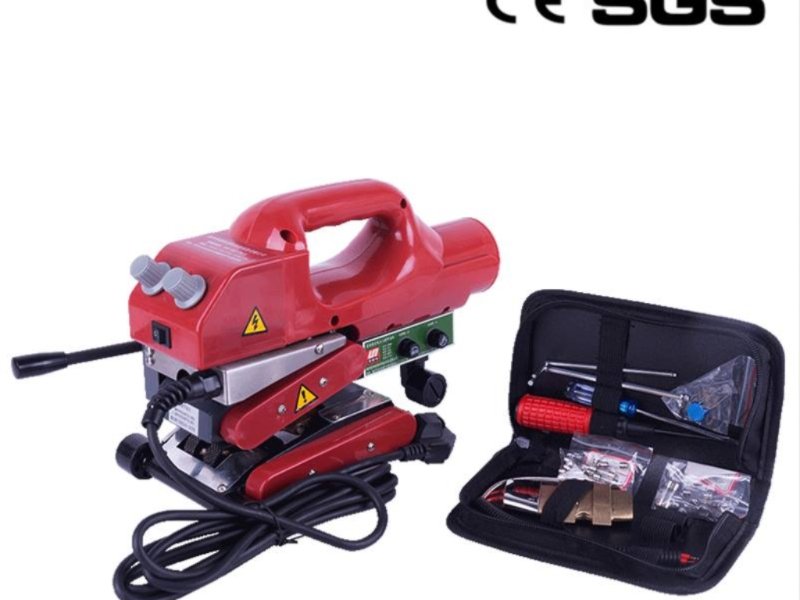
2. What Are Advantages Of HDPE Liner Welding Machine?
2.1 High-Quality Welds
HDPE liner welding machines provide uniform, high-quality welds. These welds are strong and leak-proof, essential for containment and waterproofing. The precision ensures reliable, long-lasting seams.
2.2 Efficiency and Speed
These machines offer fast welding speeds. They cover large areas quickly, reducing project timelines and labor costs. This is especially beneficial for large-scale projects like landfill liners.
2.3 Versatility
HDPE liner welding machines handle various materials and thicknesses. They are compatible with HDPE, PVC, and other thermoplastics. This versatility makes them suitable for multiple applications.
2.4 Cost-Effectiveness
By eliminating adhesives, these machines reduce material costs. They also minimize labor needs, making installation more cost-effective. Durable welds reduce maintenance and repair costs over time.
2.5 Safety and Reliability
Modern machines come with advanced safety features. These include thermal protection and emergency stop buttons. These features ensure operator safety and reliable performance.
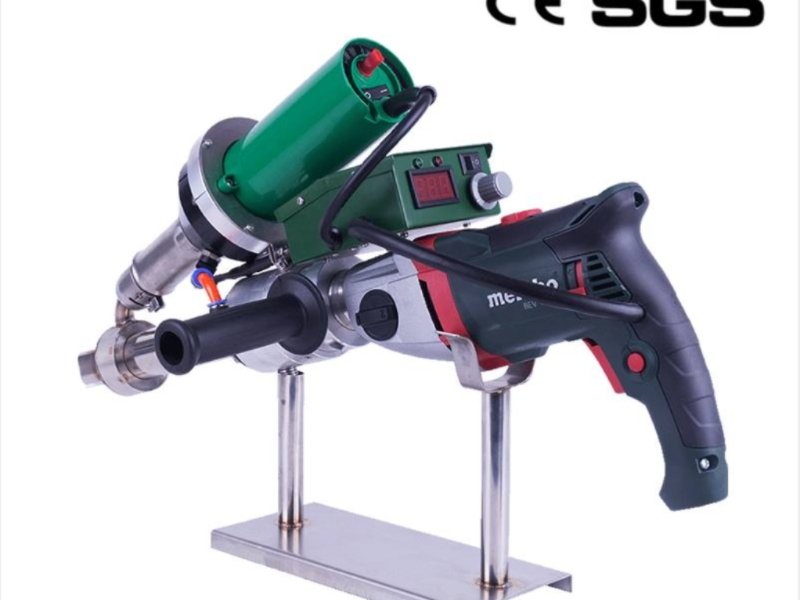
3. What Are Applications Of HDPE Liner Welding Machine?
3.1 Environmental Protection
3.1.1 Landfill Liners
HDPE liner welding machines are essential for constructing landfill liners. They create impermeable seams that prevent leachate from contaminating groundwater. This ensures environmental compliance and long-term containment.
3.1.2 Wastewater Treatment Ponds
These machines weld liners for wastewater treatment ponds. They withstand corrosive agents and ensure safe containment. Strong, leak-proof seams prevent contaminants from leaching into the environment.
3.2 Water Management
3.2.1 Reservoirs and Canals
HDPE liner welding machines line reservoirs and canals. They reduce water loss through seepage, conserving valuable water resources. This is crucial in water-scarce regions.
3.2.2 Aquaculture Ponds
In aquaculture, these machines create impermeable barriers. They maintain water quality and prevent soil contamination from fish waste. This supports healthy aquatic organism growth.
3.3 Mining and Energy
3.3.1 Heap Leach Pads
HDPE liner welding machines contain acidic or cyanide-based solutions in mining. They prevent environmental contamination and ensure regulatory compliance.
3.3.2 Oil and Gas Containment
These machines are used in secondary containment systems. They prevent spills and leaks from harming the environment.
3.4 Agriculture
3.4.1 Biogas Digesters
HDPE liner welding machines seal anaerobic digesters. They convert agricultural waste into renewable energy, preventing gas leaks.
3.4.2 Water Retention Ponds
Farmers use these machines to construct water retention ponds. They help with rainwater harvesting and irrigation, maintaining soil moisture.
3.5 Civil Engineering
3.5.1 Tunnel and Roadbed Protection
HDPE liner welding machines create waterproof barriers in tunnels and roadbeds. They prevent water infiltration, extending infrastructure lifespan.
3.5.2 Roofing and Waterproofing
These machines provide waterproof barriers in roofing systems. They protect against rainwater and snowmelt, preventing water seepage.
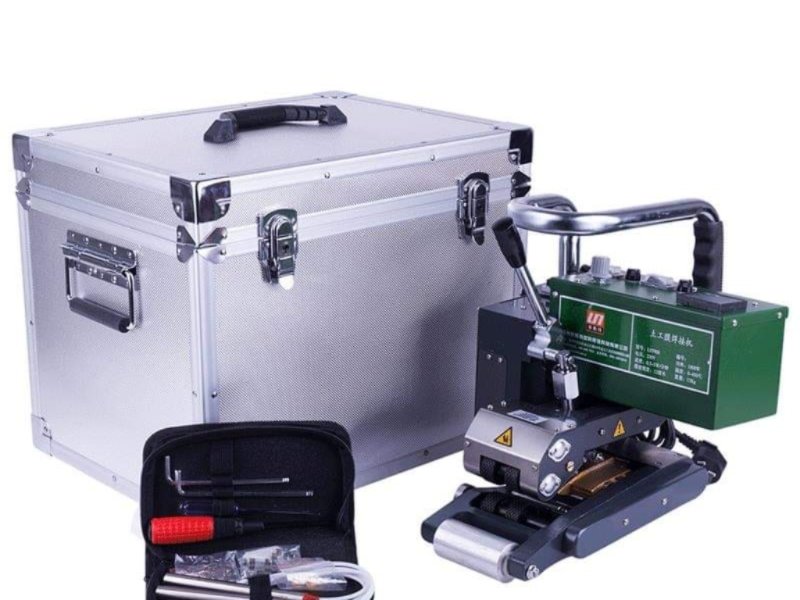
4. How To Choose Best HDPE Liner Welding Machine
4.1 Determine the Welding Method
The first step is to determine the welding method suitable for your project. There are several types of welding methods available, each with its own advantages.
4.2 Hot Air Welding
Hot air welding is versatile and portable. It uses hot air to melt the liner edges, forming a bond. This method is suitable for HDPE and PVC materials. Hot air welding machines are lightweight and easy to maneuver.
4.3 Extrusion Welding
Extrusion welding is best for thicker geomembranes. It provides strong, durable seams. This method melts the liner material and extrudes it through a nozzle. Extrusion welding machines are robust and handle thicker materials.
4.4 Wedge Welding
Wedge welding is efficient for long, straight seams. It uses a heated wedge to melt the liner material. This method is suitable for large-scale projects and provides strong, reliable welds.
4.5 Consider the Material Thickness
The thickness of the HDPE liner material is critical. Ensure the machine can handle the specific thickness. Thicker materials may require more robust machines with higher power outputs.
4.6 Evaluate Portability
If on-site welding is required, choose a machine with wheels or handles. Portability is crucial for remote or hard-to-reach areas. Lightweight and compact machines save time and effort during installation.
4.7 Temperature and Pressure Controls
Precise temperature and pressure controls are essential. A user-friendly control panel with digital displays simplifies operation. Look for machines with adjustable settings to accommodate different materials and thicknesses.
4.8 Safety Features
Safety features are crucial for operator safety. Look for machines with thermal protection and emergency stop buttons. These features reduce the risk of accidents and downtime.
4.9 Brand Reputation and Support
Choose a reputable brand with a proven track record. Reputable manufacturers offer better customer support, including technical assistance and spare parts availability.
4.10 Budget Considerations
Set a budget that balances performance, longevity, and cost. High-quality machines may have a higher upfront cost but offer better performance and durability.
4.11 Compliance and Training
Ensure the machine complies with industry standards. Arrange for proper operator training to ensure safe and effective use. Proper training enhances weld quality and reduces the risk of accidents.
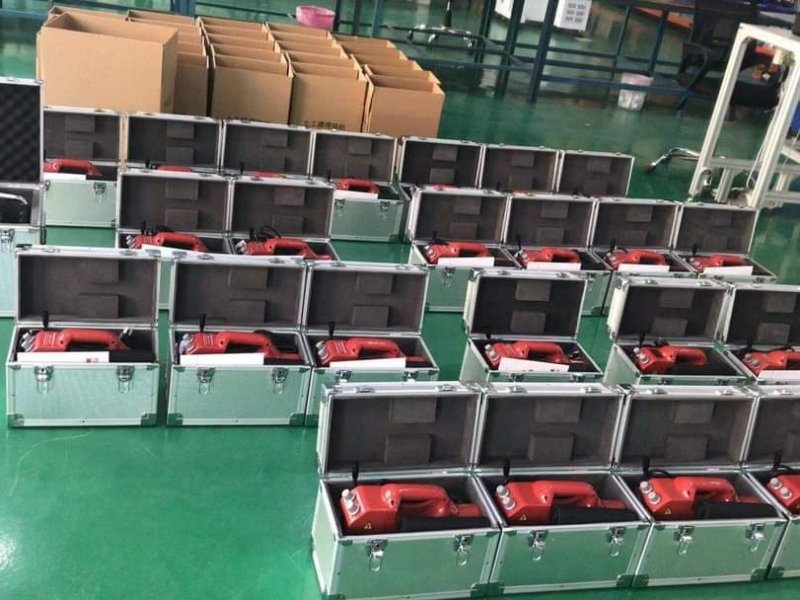
5. Summary
Choosing the best HDPE liner welding machine involves careful consideration. Determine the welding method and evaluate the machine’s ability to handle different thicknesses. Consider portability, temperature and pressure controls, safety features, brand reputation, and budget. Ensure compliance with industry standards and arrange for proper operator training. By selecting the right machine, you can ensure efficient, reliable, and safe HDPE liner installation.
6. About BPM
BPM owns a state-of-the-art manufacturing factory in Taian City, Shandong Province, China. We invested over 20 million dollars to improve production facilities, working conditions, and employee welfare. Our geomembrane factory is equipped with advanced machines and production lines. This ensures high product quality, shorter delivery times, and competitive costs.
BPM Geosynthetics is passionate about geosynthetics. We focus on new product development, enhanced testing, production, and after-sale servicing. Our team of over 100 professionals serves clients worldwide. We offer customization services, including ODM and OEM options, to meet your specific requirements.